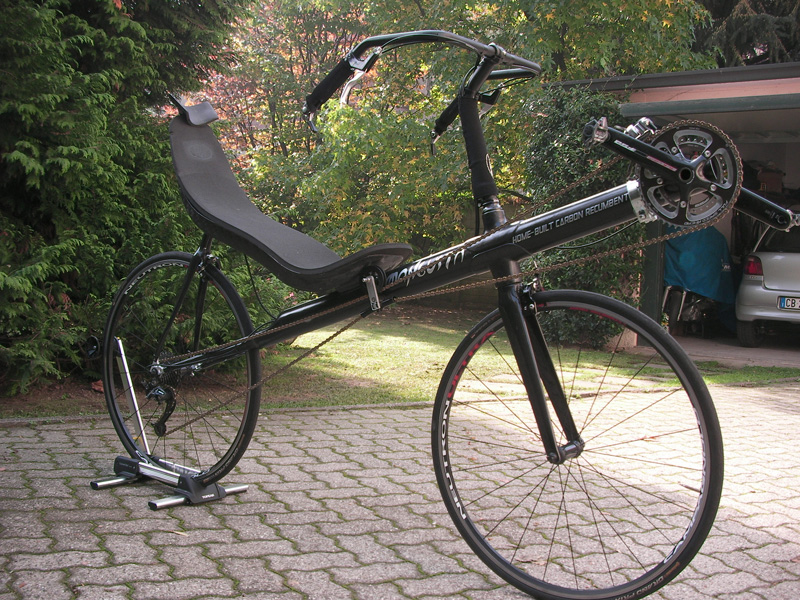
Il "progetto MANGUSTA" nasce dalla volontà di realizzare una reclinata autocostruita che mi permettesse di esercitarmi nella laminazione del carbonio e che mi desse la soddisfazione di poter utilizzare un mezzo costruito con le proprie mani.
Per evitare le incognite di un progetto originale e magari inusuale, ho deciso di clonare un modello commerciale molto apprezzato, anche se non particolarmente diffuso, che potesse rispondere a determinati requisiti, senza creare troppi problemi o sorprese.
Uno dei requisiti principali, era quello di perseguire la maggior rigidità possibile del telaio e l'ottimizzazione della linea catena, in modo da rendere il trasferimento di potenza, dai pedali alla ruota, il più efficiente possibile. Insomma, volevo una bent che rispondesse al colpo di pedale, come una bdc, da questo punto di vista, molto avvantaggiata, con i suoi triangoli e con il carro cortissimo. Basti pensare ai 40 cm. tra il movimento centrale e mozzo di una bdc, contro il metro e mezzo di una reclinata, per di più, con un monotrave senza triangolazioni.
La "Carbent Raven" era il modello che meglio interpretava questi requisiti.
Telaio dritto, sedile integrato nella struttura del telaio a formare il triangolo posteriore, linea catena di pochissimo angolata e che passa all'interno del carro posteriore, allineata con l'asse del tubo principale.
Per esaltare ancor di più queste caratteristiche, ho deciso di non dare troppa importanza al peso e fare dei componenti surdimensionati negli spessori. Quanto possa influenzare il peso in salita, è cosa risaputa e verificata. Si tratta di secondi (non minuti) per ogni chilo, per mille metri di dislivello.
Quanto possa influenzare la rigidità del telaio e la linea di catena, non lo sappiamo e per andare sul sicuro ho preferito abbondare con gli strati di carbonio, tenendo anche presente che una laminazione manuale, non ha le stesse caratteristiche di quella fatta con pre-impregnati e autoclave.
Per gli stessi motivi ho deciso di costruire sia il sedile sia il boom, nonostante ci fosse la possibilità di utilizzare componenti commerciali, mentre, ho acquistato il carro posteriore, il tubo di sterzo e la forcella, tutti di origine Dedacciai.
Il carro, in origine, è destinato ad essere incollato ad un telaio in alluminio, mentre la forcella è una full carbon, cannotto conico, 1" e 1/8 superiormente, 1" e 1/2 inferiormente, giusto per complicarsi un po' la vita.
L'idea originaria era di fare un tubo principale composto da due parti, una interna sottile, da unire, senza incollare, alla parte interna carro posteriore basso, tramite un raccordo in carbonio leggermente angolato e poi laminare al di sopra il resto degli strati mettendo il tutto nel sacco del vuoto.
Facendo alcune prove con fibra di vetro, mi sono reso conto che il tubo primario, quello più interno, non poteva essere troppo sottile, perché si sarebbe deformato con la pressione esercitata dal sacco del vuoto, inoltre mettendo i pezzi in dima, ho appurato che non era necessario angolare il tubo principale con il carro basso per non interferire con la catena, ma si poteva tenerlo allineato, pur con la catena che sfiorava il carbonio. Nella Carbent originale, infatti, il forcellino Deda, viene sostituito da un altro fatto al CNC, che permette di alzare il perno del mozzo e allontanare la catena dal fodero orizzontale del carro posteriore. Per cui ho fatto un tubo principale primario, laminando 4 strati di carbonio su di un tubo arancione da edilizia, diametro 63 mm, e mettendo il tutto sotto vuoto. Purtroppo, durante la fase del vuoto, si sono manifestati alcuni inconvenienti, in particolare, siccome mi ero dimenticato di tappare le estremità del tubo, il sacco veniva risucchiato all'interno, poi, il sacco stesso, stringendosi attorno al tessuto aeratore, formava delle grinze, che in parte si trasferivano anche ai tessuti sottostanti. Il risultato è stato un tubo un po’ grinzoso, che ho deciso di non rifare, ma di carteggiare per togliere le pieghe, anche se ciò ha comportato un indebolimento dello stesso. Tanto, questo tubo sarebbe servito da anima per quello principale e avrebbe fornito la posizione al carro posteriore.
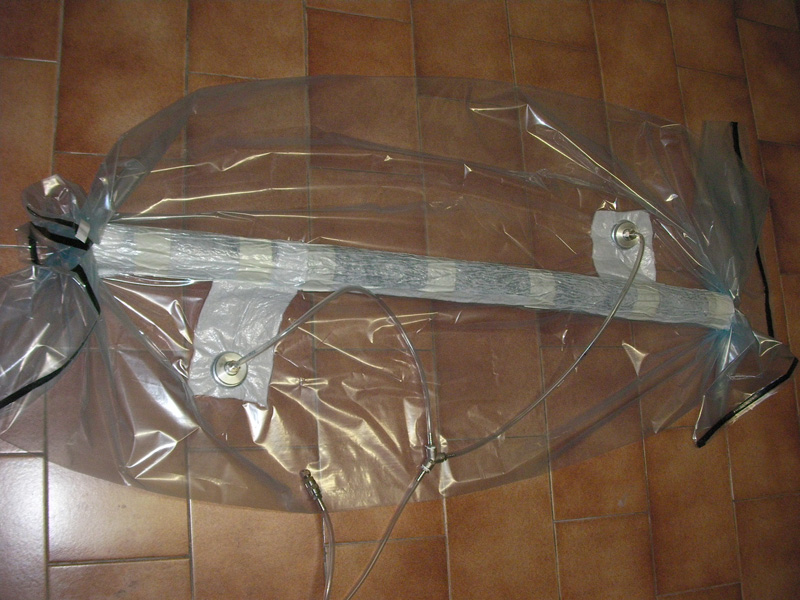
Il passo successivo è stato quello di fare un raccordo in polistirene ricoperto di carbonio tra l'interno del tubo e l'interno del carro, con adesione al tubo ed isolamento dal carro, in modo da poterlo sfilare.
Poi, laminazione del tubo principale su quello primario e sull'esterno del carro, in modo da ottenere un tubo definitivo che avesse nella parte anteriore un diametro interno esatto per alloggiare il boom e, nella parte posteriore, una doppia parete che potesse essere incollata sia all'interno, che all'esterno della base del carro.
La laminazione è stata fatta manualmente, senza applicazione del vuoto, per evitare la formazione di grinze. Avevo previsto anche uno strato finale in tessuto 3k, a scopo estetico, ma alla fine ho rinunciato, perché il tubo aveva già uno spessore eccessivo.
Naturalmente ho dovuto accettare la presenza di numerosi buchini che si formano tra le fibre e che risulta molto laborioso eliminare. A lavoro finito, prima della verniciatura, ho stuccato solo quelli più evidenti.
La separazione del tubo principale dal carro, nonostante l’abbondante uso di distaccante e nastro isolante, non è stata agevole. Ho dovuto mettere in trazione i due pezzi sul tavolo da falegname, dopo averli imbragati con fettuccia da alpinismo.
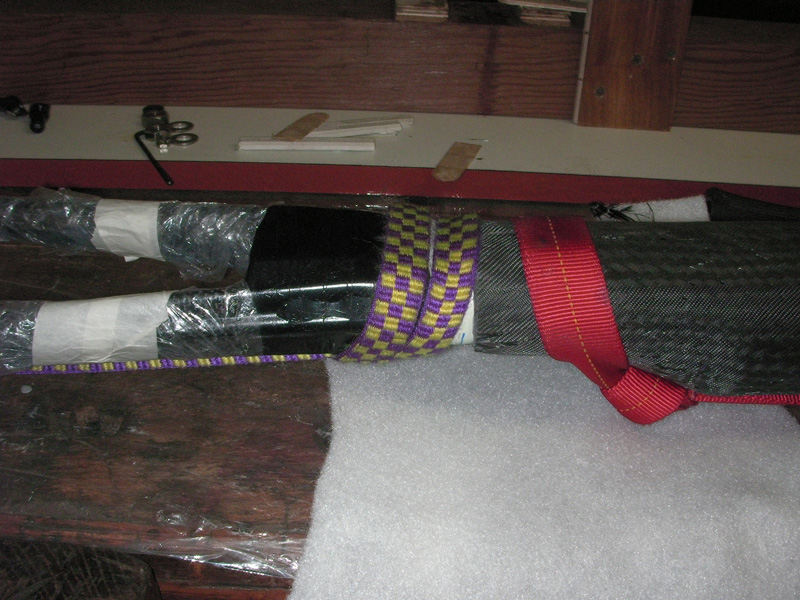
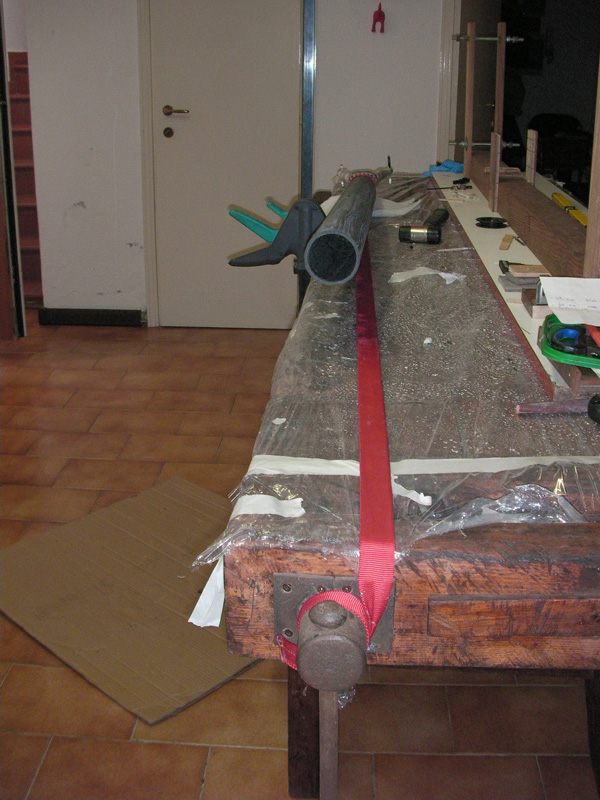
LA PROVA DI CARICO
Prima di proseguire con le successive fasi di costruzione, ho fatto una prova di carico per testare la resistenza e la deformazione del tubo, lungo 120 cm. Per fare ciò, ho costruito un supporto costituito da uno scatolato in ferro 10x10 e due travetti in legno della stessa misura, uniti a formare una U. Il tubo, appoggiato alle estremità sgolate dei travetti, è stato agganciato sulla metà con una fettuccia da roccia e messo in trazione col tramite di un dinamometro dalla portata massima di 300 kg. Nella foto si legge il carico di 263 kg, ma la trazione aveva raggiunto i 300 kg, solo che il nodo della fettuccia si rilasciava leggermente per la tensione e, tempo di prendere la macchina foto, il valore si era già abbassato. La flessione misurata dal tubo ad una trave in acciaio del soffitto della cantina, è di circa 2 mm.
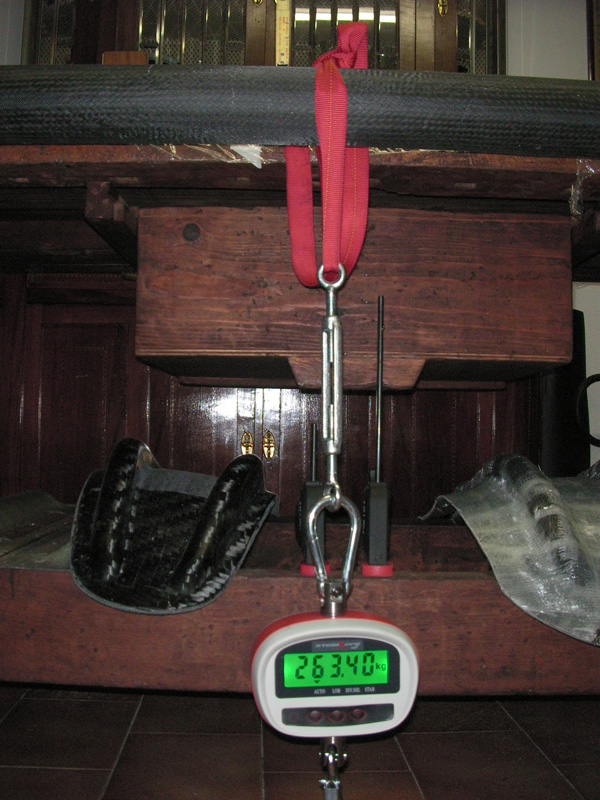
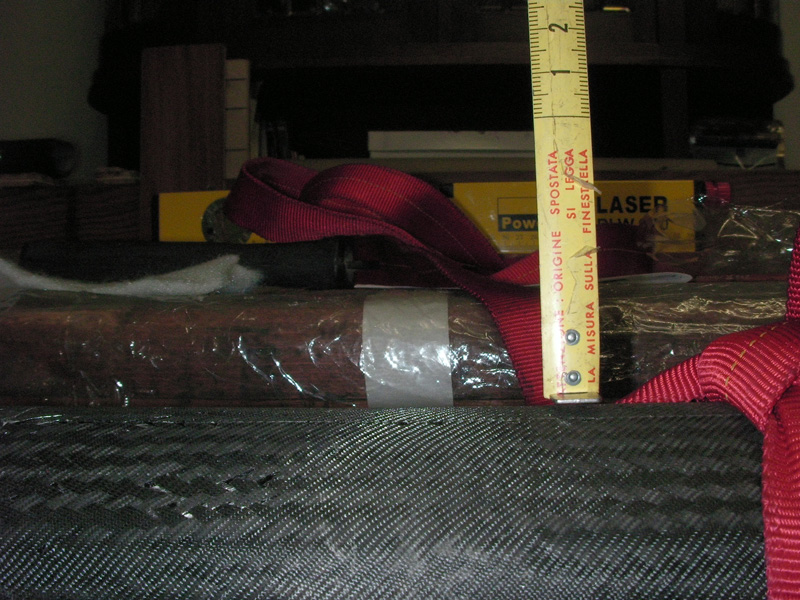
Vediamo ora le altre parti che, insieme al tubo principale, vanno a costituire il telaio:
IL SEDILE
Il sedile è stato ottenuto facendo lo stampo di un originale M5.
Lo stampo è servito per laminare e polimerizzare sotto vuoto, il guscio inferiore.
Poi è stata laminata la parete superiore, sempre col vuoto, dopo aver riempito con schiuma poliuretanica, le cavità delle nervature. Avevo pensato anche ad altre metodiche per evitare di lasciare la schiuma all'interno, ma questa mi sembrava la più veloce. Purtroppo non avevo a disposizione del gelcoat, perché, con lo stampo, la superficie esterna risulta già molto ben rifinita, ma col gelcoat, non avrebbe neppure bisogno di verniciatura. Naturalmente, sia nella costruzione dello stampo, che nella laminazione, bisogna essere molto attenti nell'utilizzo degli isolanti-distaccanti, pena la perdita del modello, dello stampo o del pezzo.
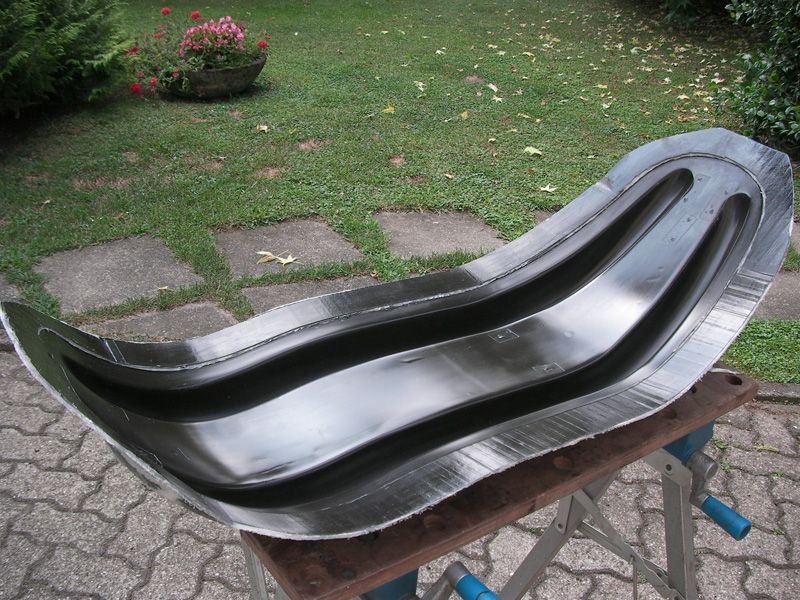
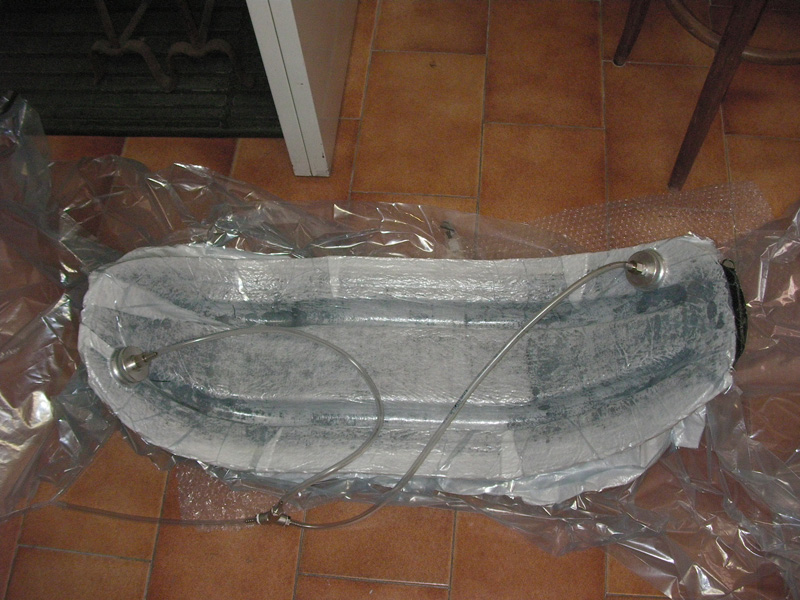
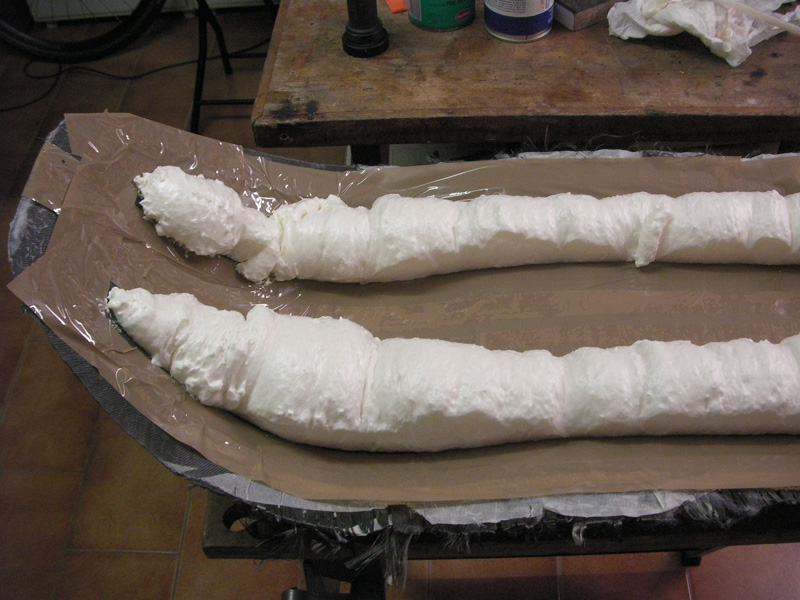
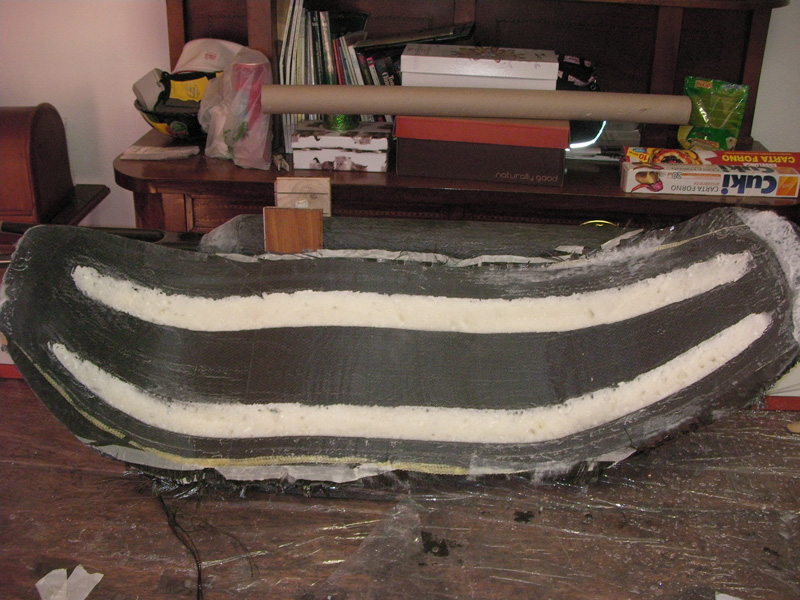

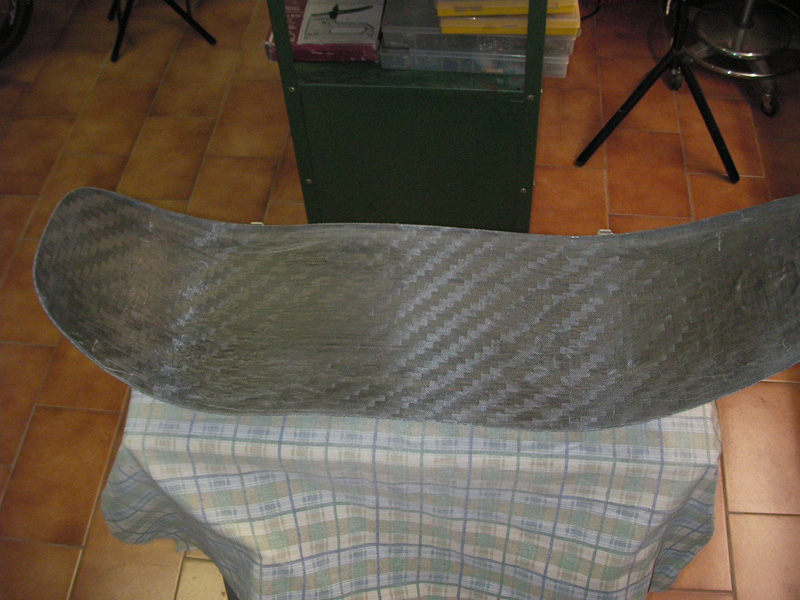
IL BOOM
Il boom è stato ottenuto facendo uno stampo in due semigusci, di un tubo pvc da 63 mm.
Gli trati di carbonio sono stati laminati su di un tubo leggermente più piccolo di diametro e poi posti nello stampo con una camera d'aria da mtb, opportunamente tagliata e sigillata, all'interno. Una volta chiuso lo stampo, mettendo in pressione la camera d'aria, gli strati di carbonio scivolano e si espandono contro le pareti. La pressione va mantenuta sino a polimerizzazione completata e il risultato sarà un tubo con diametro esterno esatto, che si potrà inserire nel telaio.
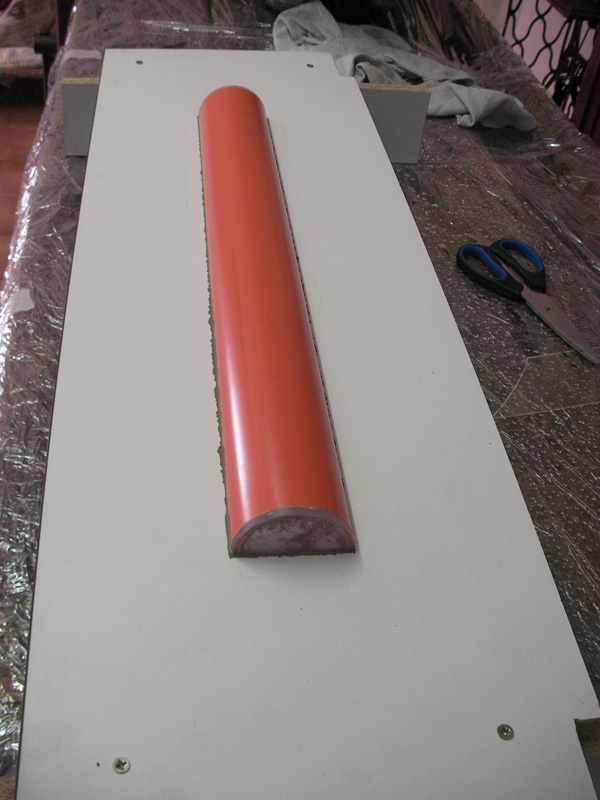
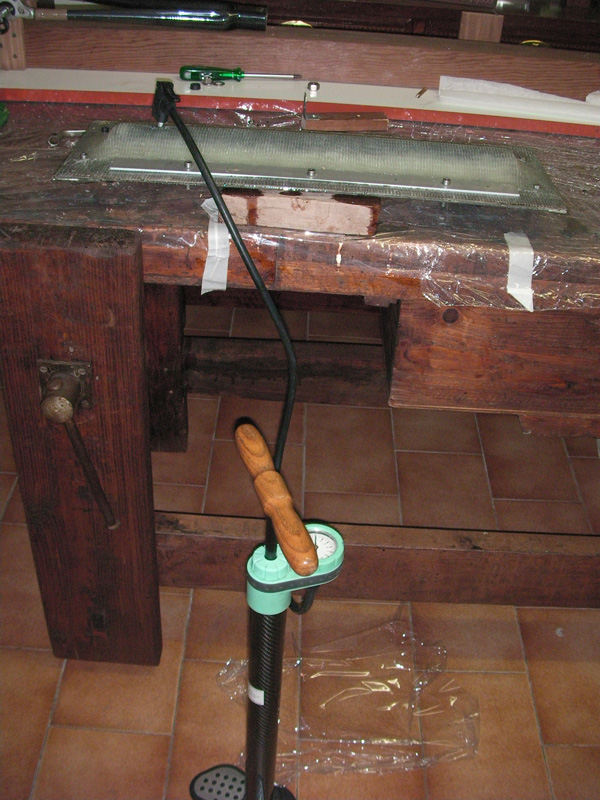
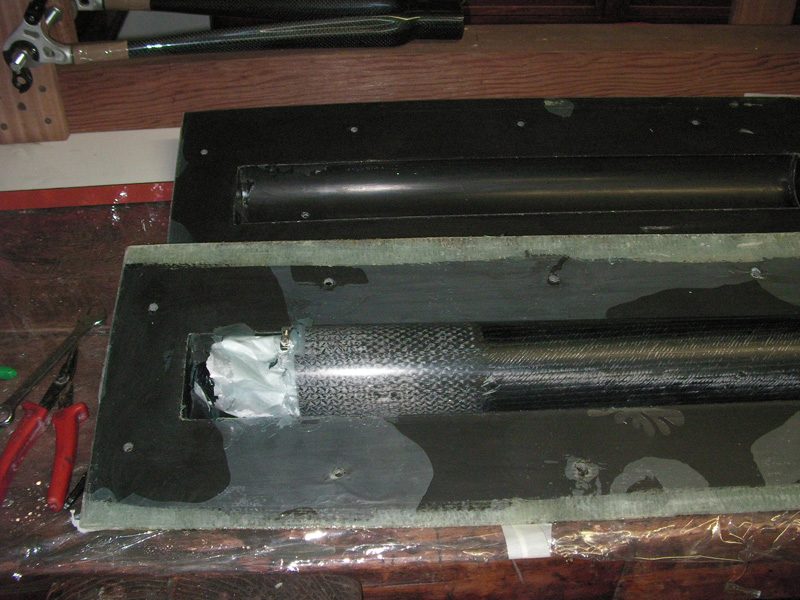
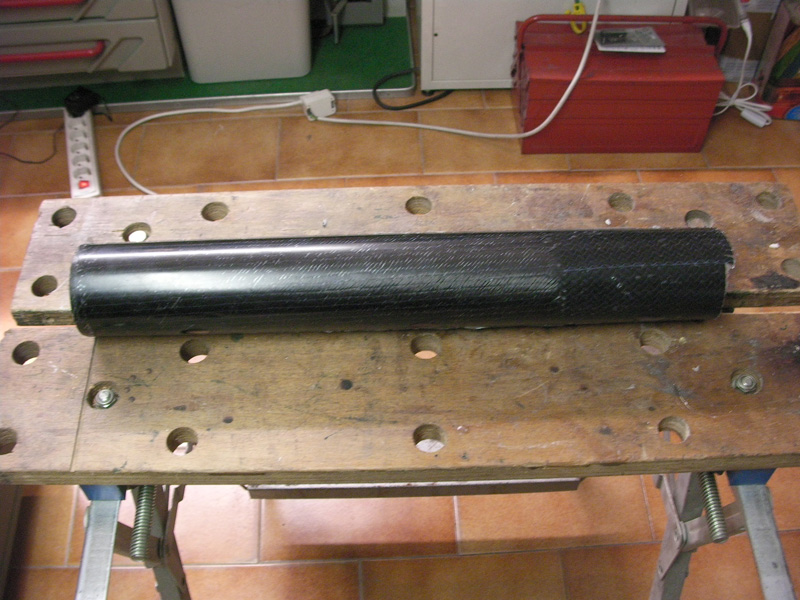
Con una fresa a tazza, si esegue il foro per il movimento centrale, dopo aver bloccato il tubo su di una dima e sul piano del trapano a colonna.
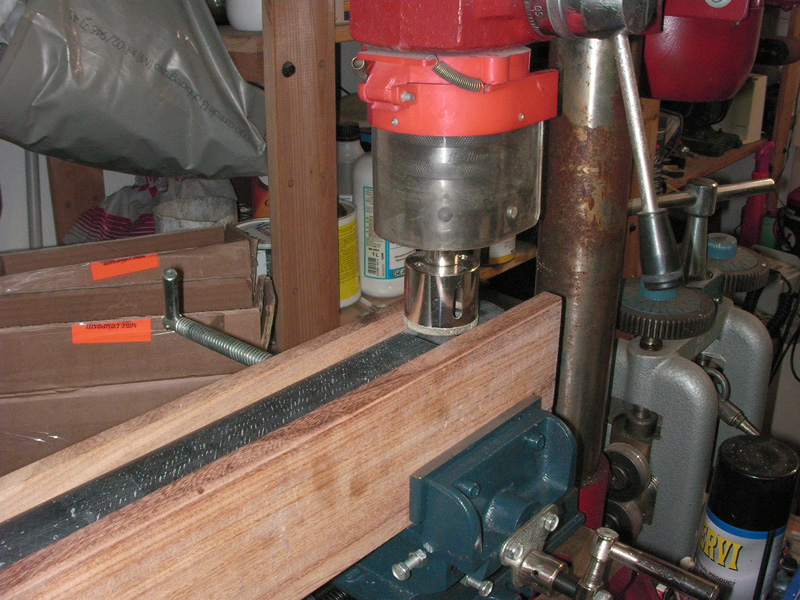
Il tubo in alluminio del MC, viene rivestito in fibra di vetro e poi incollato, dopo averlo posizionato in dima. Successivamente, viene spinto tessuto di carbonio e un mix di epossidica con sfioccato di cotone, davanti e dietro al tubo del MC, per mezzo di due pistoni sagomati in polistirene+pellicola isolante. Ciò consente di fare un blocco tra MC e boom.
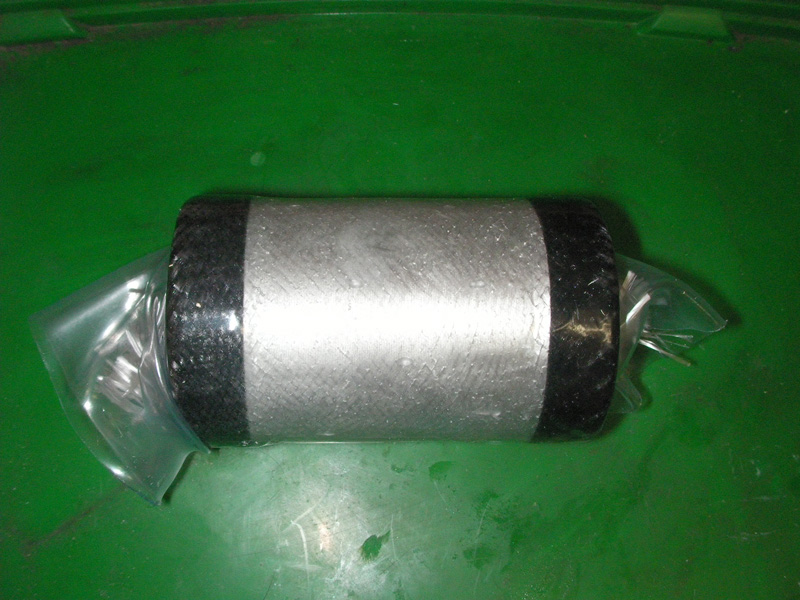
Per completare il boom, si incolla alla giusta inclinazione un pezzo di tubo da 1" e 1/8, recuperato dal taglio di una forcella. Ad incollaggio terminato si rinforza la giunzione con tessuto di carbonio e stucco strutturale (epoxi+sfioccato di cotone). Con lo stesso procedimento ho fatto la sede del perno della puleggia, in modo da non dover bucare il tubo del telaio.
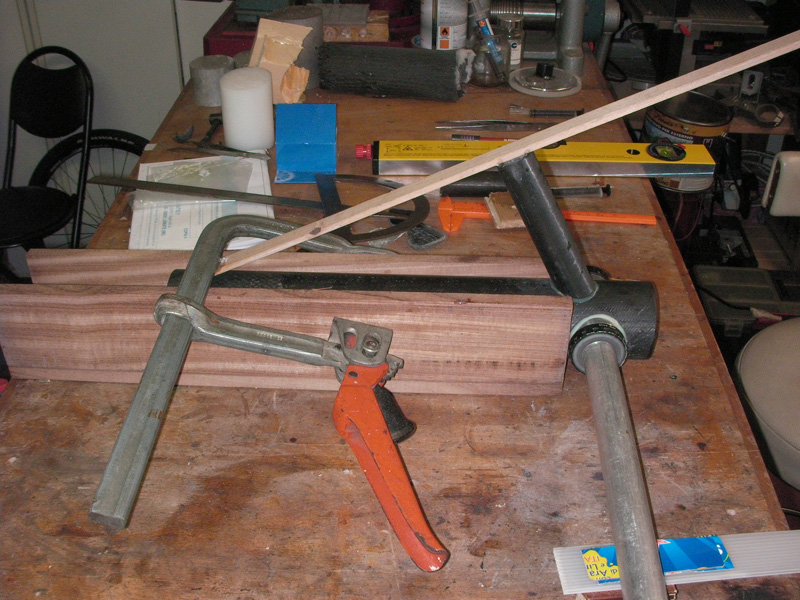
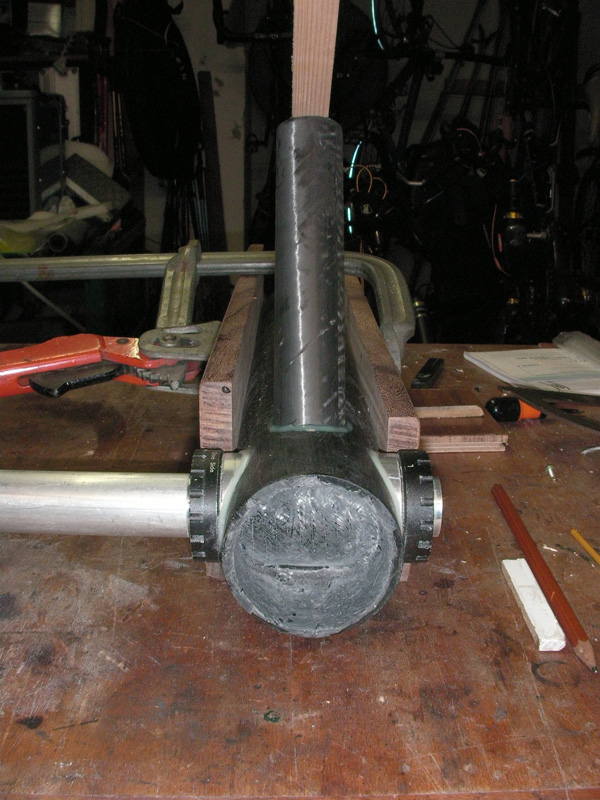
Per completare il boom, si incolla alla giusta inclinazione un pezzo di tubo da 1" e 1/8, recuperato dal taglio di una forcella. Ad incollaggio terminato si rinforza la giunzione con tessuto di carbonio e stucco strutturale (epoxi+sfioccato di cotone). Con lo stesso procedimento ho fatto la sede del perno della puleggia, in modo da non dover bucare il tubo del telaio.
Ora è la volta delle congiunzioni che permetteranno l'unione del sedile e del tubo di sterzo al telaio.
LE CONGIUNZIONI
Le due congiunzioni del tubo di sterzo, che servono anche da rinforzo del telaio in una zona dove sono stati fatti due fori di grande diametro, sono state abbastanza laboriose da fare e da incollare.
Per prima cosa bisogna approntare una dima che permetta di fissare il tubo del telaio al piano del trapano a colonna, con una inclinazione di 8° e poi fare due fori centrati e coassiali di diametro diverso, poiché il tubo di sterzo è conico.
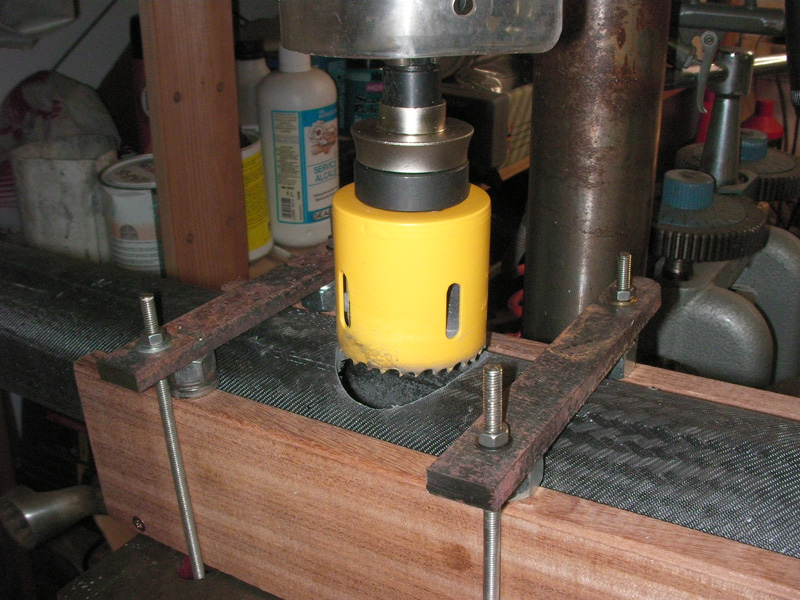
In seguito si fissa il tubo di sterzo al telaio con punti di stucco epossidico, dopo aver montato forcella e movimento, in modo da avere una posizione esatta in dima. Si esegue la laminazione degli starti di carbonio attorno alla parte superiore del tubo di sterzo, alternati e parzialmente sovrapposti a quelli sul tubo telaio, poi si mette il tutto in pressione con termo restringente e controforma.
Si ottiene così la congiunzione superiore che può essere sfilata verso l’alto. Quella inferiore, una volta laminata e polimerizzata, essendo costruita su di un tubo conico, andrà tolta dal telaio insieme al tubo di sterzo, dopo averlo separato dai punti di fissaggio in stucco epoxi.
Per la stessa ragione, ovvero per la conicità del tubo di sterzo, l’incollaggio delle congiunzioni, andrà fatto in un unico passaggio, incollando congiunzioni, telaio, tubo di sterzo e sedi metalliche dei cuscinetti; il tutto con la forcella e il movimento montati e messi in tensione, isolati da eventuali infiltrazioni di adesivo strutturale e bloccati in dima.
Congiunzione inferiore
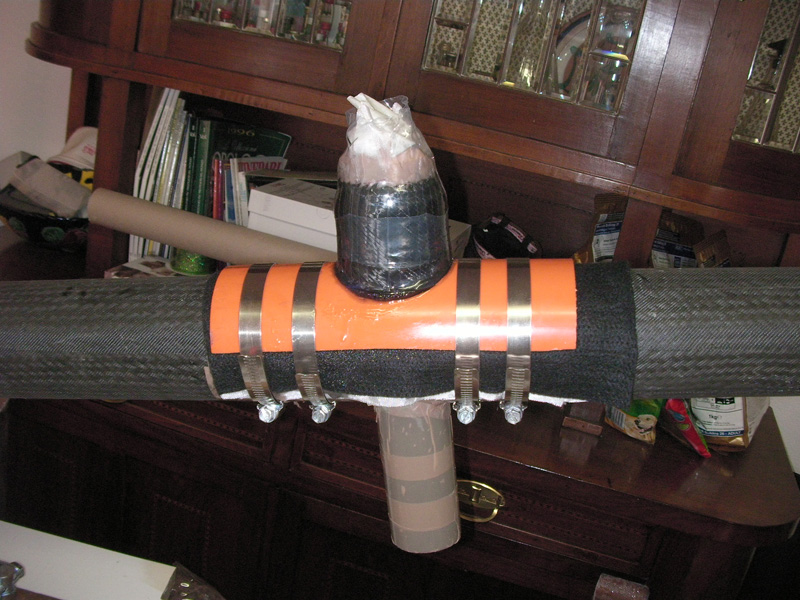
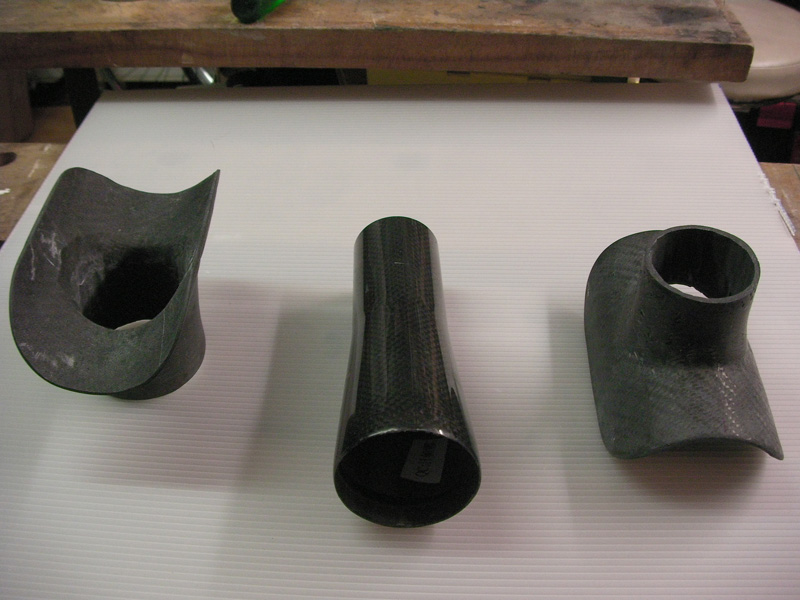
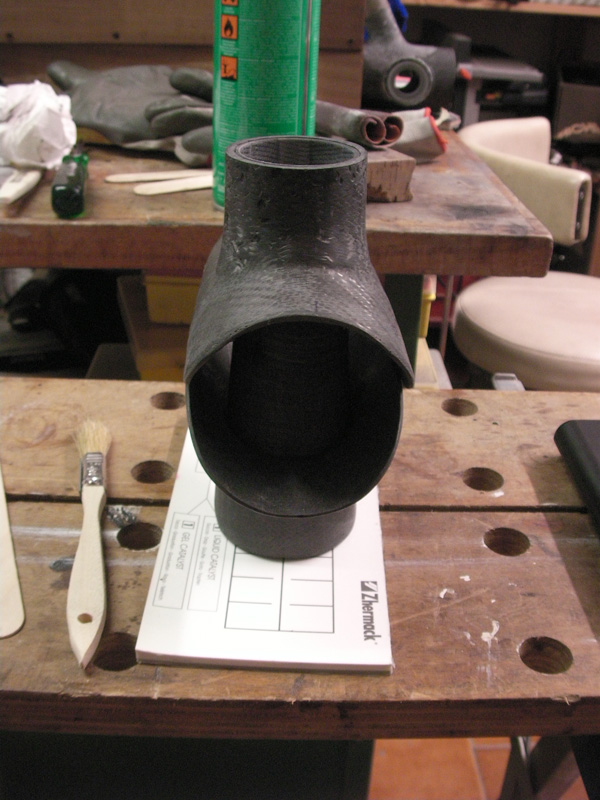
La congiunzione inferiore del sedile, si ottiene laminando il carbonio attorno a due forme in gomma siliconica, corrispondenti ai due canali vuoti, e tra il tubo telaio e il fondo del sedile opportunamente isolati. Le forme in gomma siliconica, sono state ottenute premendo la gomma in fase malleabile, tra il telaio e il sedile con l’interposizione di lastre in cera a spessore costante di 2 mm, opportunamente sagomate dopo essere state scaldate sino a renderle modellabili.
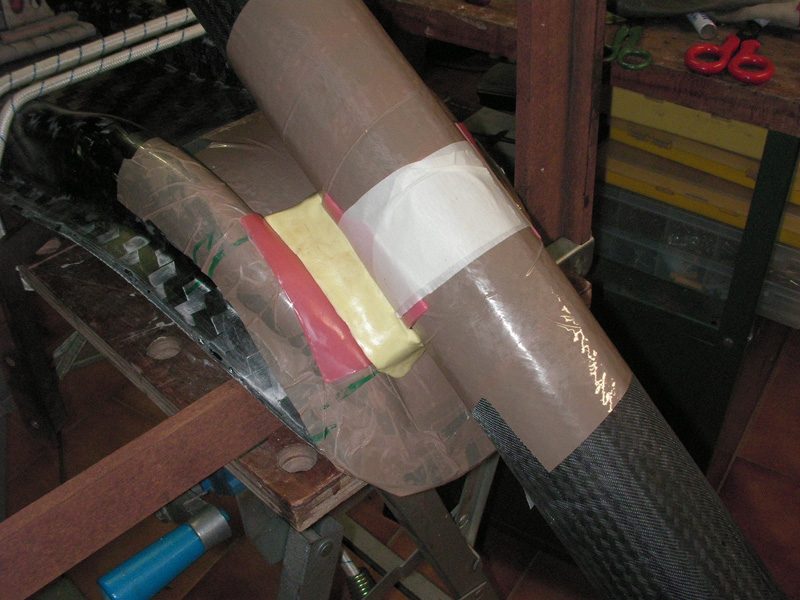
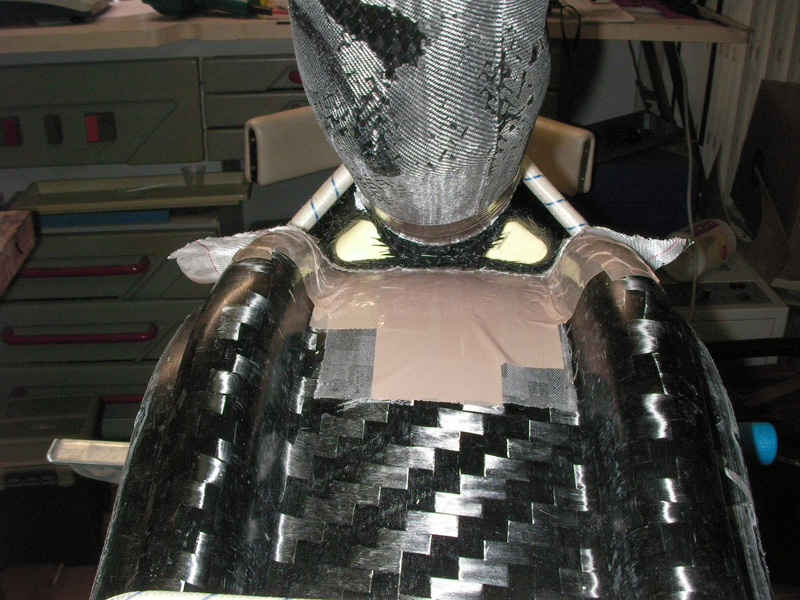
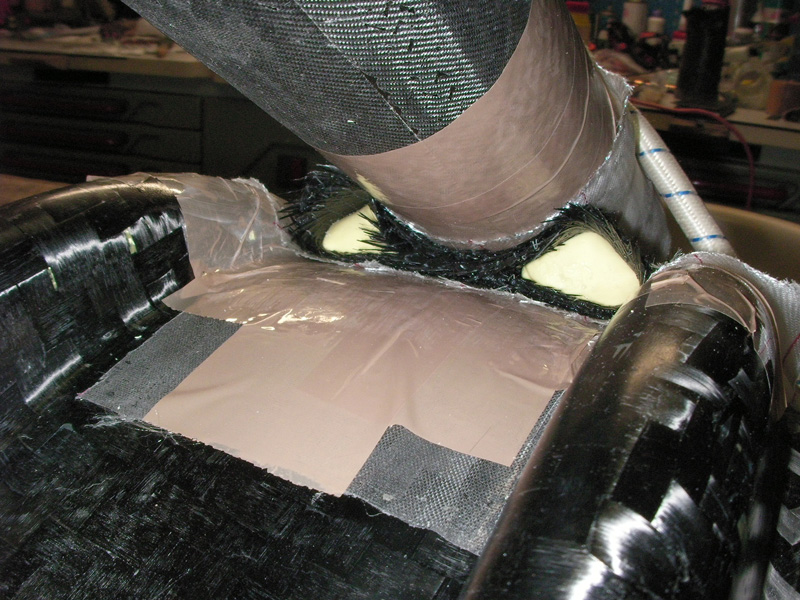
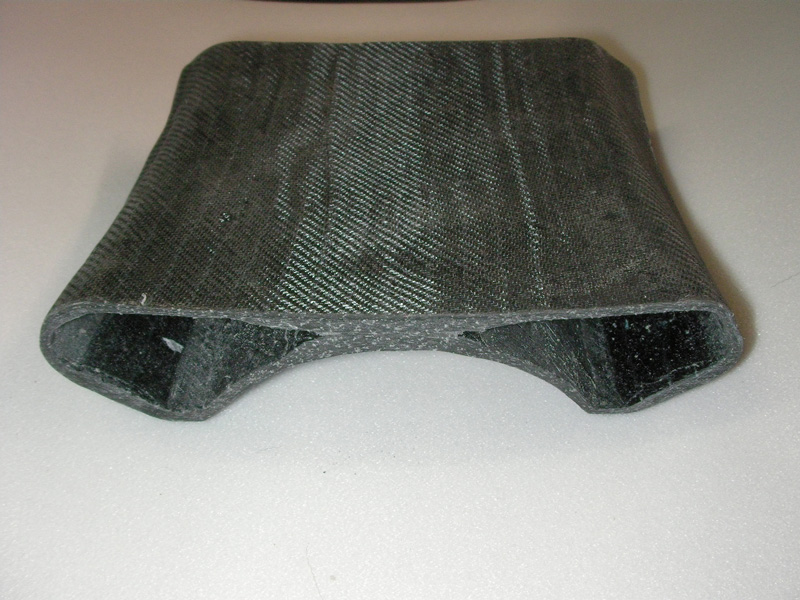
La congiunzione superiore si ottiene facendo prima due parti, una attorno al tubo del carro, l’altra sul fondo del sedile. Si incollano i due pezzi dopo averli posizionati in dima e si finisce con un’ulteriore laminazione di carbonio. L’incollaggio delle congiunzioni con telaio e sedile sarà ultimato dopo aver fissato il tubo principale al carro e allo sterzo.
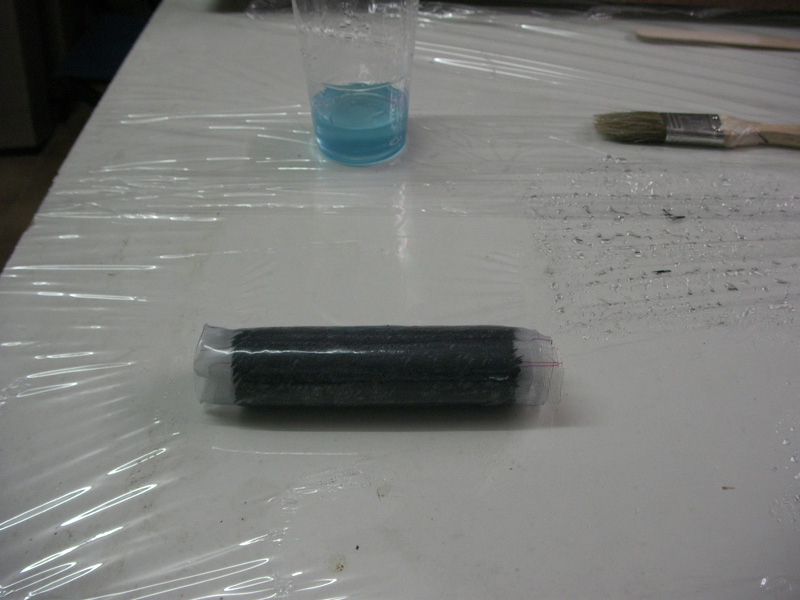
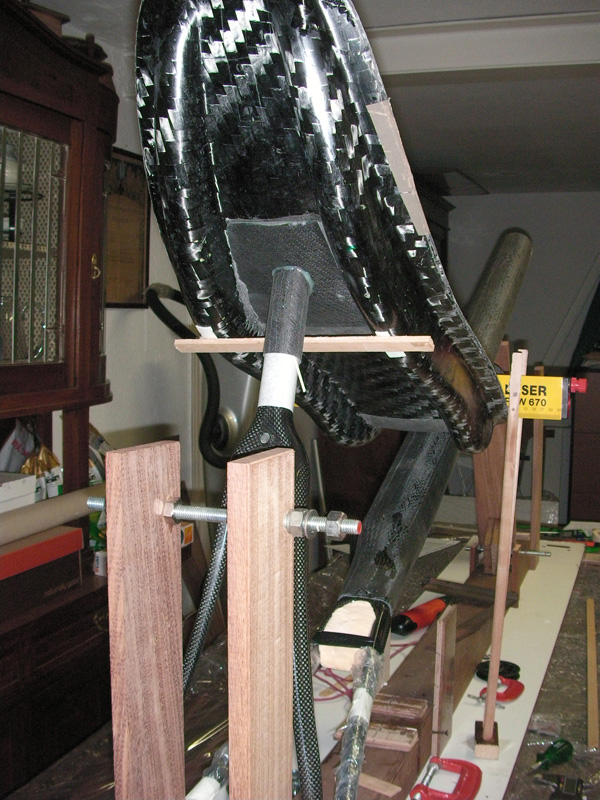
BATTICATENA
Terminato il montaggio della reclinata, ho potuto verificare meglio il passaggio della catena rispetto ai foderi orizzontali del carro. La catena non interferisce col telaio finché rimane in trazione, può battere sul carbonio solo quando ci sono dei sobbalzi con la catena non in tensione. Per evitare di rovinare il telaio, ho deciso di modellare un batti - catena in tessuto di kevlar, direttamente sul tubo e, dopo averlo rifinito, l’ho incollato. Il kevlar è giallastro e per mimetizzarlo meglio, l’ho laminato con resina epossidica e pigmento nero. Purtroppo il kevlar è difficile da rifinire perché la fresatura e la carteggiatura, provocano lo sfilacciamento del tessuto, che è molto tenace. Per questo i bordi del batti-catena sono rimasti un po’ irregolari.
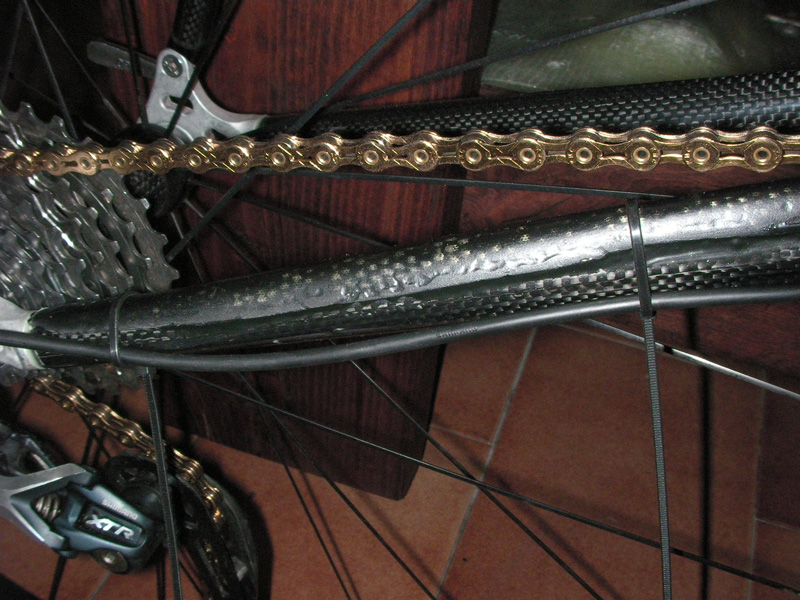
IL POGGIATESTA
Usando un sedile molto inclinato, il poggiatesta, o poggia nuca, diventa indispensabile e deve essere comodo ed anatomico, senza interferenze col casco.
Per farlo il più aderente possibile, ho preso una specie d’impronta della zona nucale, usando una lastra di cera ammorbidita col calore, ponendola a contatto con la nuca, sino al suo consolidamento.
Sulla base della forma, ho costruito un piccolo stampo e poi ho laminato la zona di appoggio.
Il gambo, invece, è stato fatto con 4 strati di carbonio+1 di kevlar, irrigiditi da due nervature ottenute con un’anima di polistirene.
Le due parti, appoggio e sostegno, sono state unite fissando il gambo al sedile e incollando provvisoriamente l’appoggio con la testa in posizione. Il tutto è stato poi unito definitivamente con stucco strutturale e tessuto in carbonio.
In seguito ho ricavato delle asole, al posto dei buchi, in modo da poterlo spostare in verticale. Da notare che l’appoggio può scendere anche al di sotto del limite superiore del sedile.
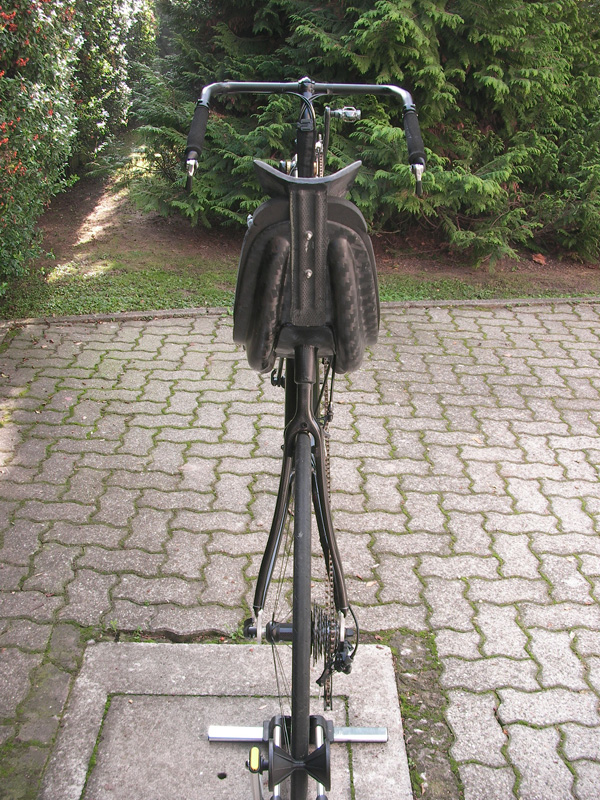
Il fissaggio del boom scorrevole col telaio è ottenuto per mezzo di un grosso morsetto in metallo. La forza che deve fare è notevole, perché il tubo del telaio spesso 4 mm , non cede tanto facilmente. Pensavo, però, di costruire un morsetto in carbonio e viti in metallo.
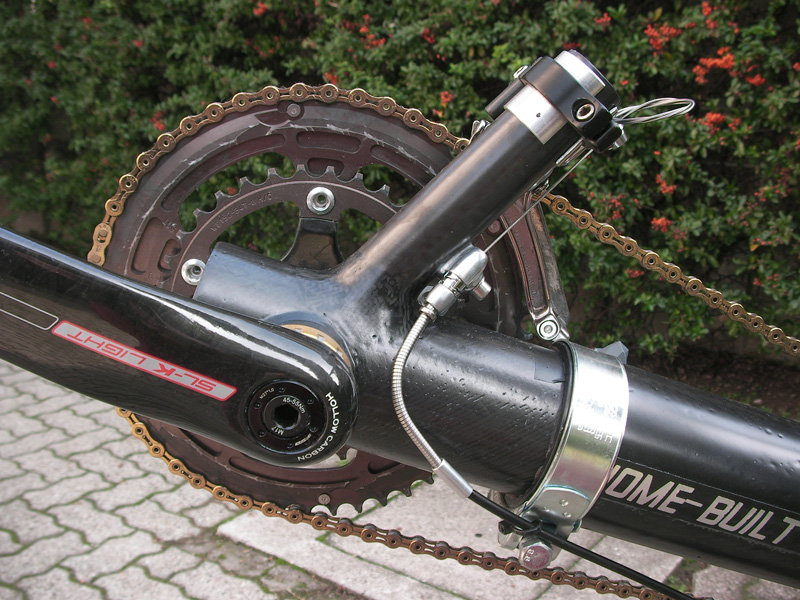
Anche la parte terminale del boom riceverà presto un supporto per il fanale, da nascondere, quando non in uso, con un tappo a forma di ogiva.
Gli incollaggi sono stati eseguiti con adesivo epossidico strutturale Shaller e Loctite 9466. Il primo è molto denso e difficilmente miscelabile col catalizzatore. L’ho utilizzato negli incollaggi dove c’era più spazio tra i pezzi. Quello della Loctite, consigliatomi da Marcosan che lavora nel settore, si presenta in cartuccia a due vie ed è abbastanza fluido e facilmente miscelabile anche a mano, senza utilizzare le apposite cannule.
Quest’ultimo l’ho utilizzato per gli incollaggi più critici, in particolare quelli tra metallo e carbonio.
La verniciatura mi ha creato qualche difficoltà. L’intenzione era di dare un fondo epossidico e poi una finitura poliuretanica. Come fondo ho utilizzato il top coat epossidico, stessa marca della resina da laminazione. Il top coat fornisce uno strato lucido, molto duro e resistente.
Fatte delle prove su di un campione, sembrava che tutto andasse bene, ma, una volta iniziata la verniciatura del telaio, sono iniziate le sorprese. Per prima cosa, ho voluto verniciare a spruzzo pur non essendoci indicazioni in tal senso nella scheda tecnica. Sia la regolazione della pistola, che la diluizione della vernice, erano molto difficoltose e il risultato era una superficie irregolare e a buccia d’arancia. Per di più, i piccoli forellini presenti sulla superficie del carbonio, venivano dilatati a dismisura dalla vernice, che sembrava ritirarsi attorno ad essi. Per cui, carteggiatura e stuccatura delle piccole irregolarità. Poi verniciatura a pennello con top coat addizionato ad un componente tixotropico.
La verniciatura sembrava venuta bene, ma, dopo un adeguato tempo di asciugatura, un’ulteriore sorpresa.
Il top coat non era indurito! Vado subito a verificare i contenitori della resina e mi rendo conto di aver pesato due volte lo stesso componente, invece di resina+catalizzatore! Mi tocca togliere tutta la resina non catalizzata e pulire bene con solvente. La successiva stesura del top coat non ha dato luogo ad inconvenienti, ma il risultato finale era una superficie molto lucida che non mi piaceva.
Per questo motivo, la successiva verniciatura è stata eseguita con trasparente poliuretanico semilucido. La riuscita è stata soddisfacente, anche se non paragonabile a quella del gelcoat nello stampo o ad una verniciatura pigmentata dopo stuccatura pesante. Infatti, per lasciare trasparire la trama del tessuto di carbonio, la stuccatura deve essere sempre leggera.
Termino qui questa semplice relazione sulla mia autocostruzione, anche se ci sarebbero molte altre cose da dire. Il tipo di montaggio e i componenti possono essere dedotti dalle foto. Qualche numero per avere un’idea del dimensionamento del telaio.
Interasse:120cm.
Inclinazione sedile:20°
Angolazione tubo di sterzo: 72°
Altezza seduta:65cm.
Peso:?????? Diciamo che il peso in ordine di marcia, con pedali, poggiatesta, cuscino è pari a quello della M5 midracer montata XT+tripla, cioè 11kg.
La maggior parte dei materiali sono stati acquistati on line da HP-Textiles
www.hp-textiles.com/shop/index.php?...a96a2a495903#98e da Shaller
www.schaller-compositi.it/ecomm/site.php?mode=LST&cat=50Comunque, il progetto Mangusta non è ancora terminato e prosegue con la costruzione di un codino aerodinamico e la sperimentazione di un variatore di assetto.
Le impressioni d’uso le metterò più avanti in un altro post.
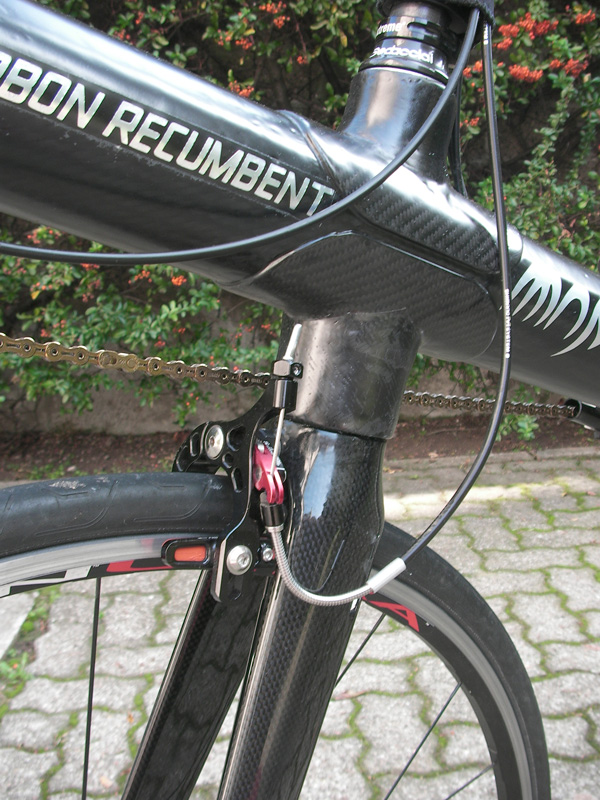
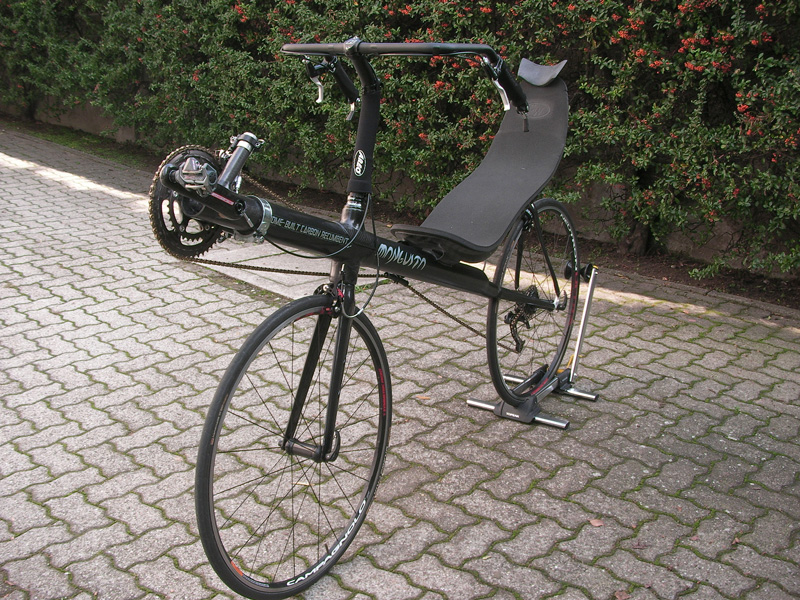
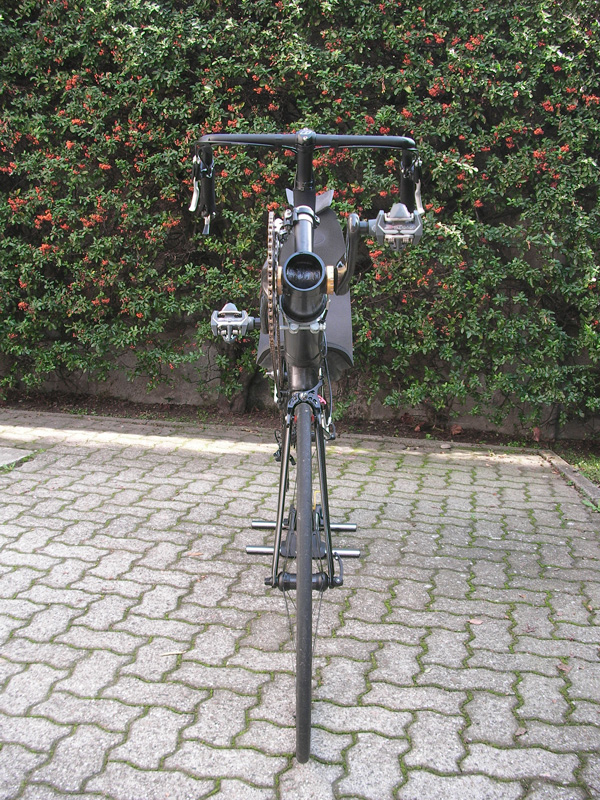
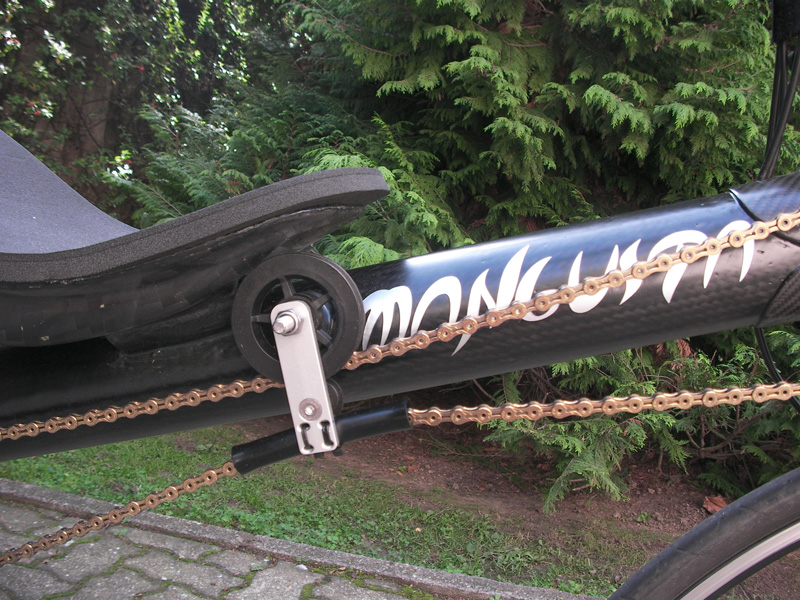
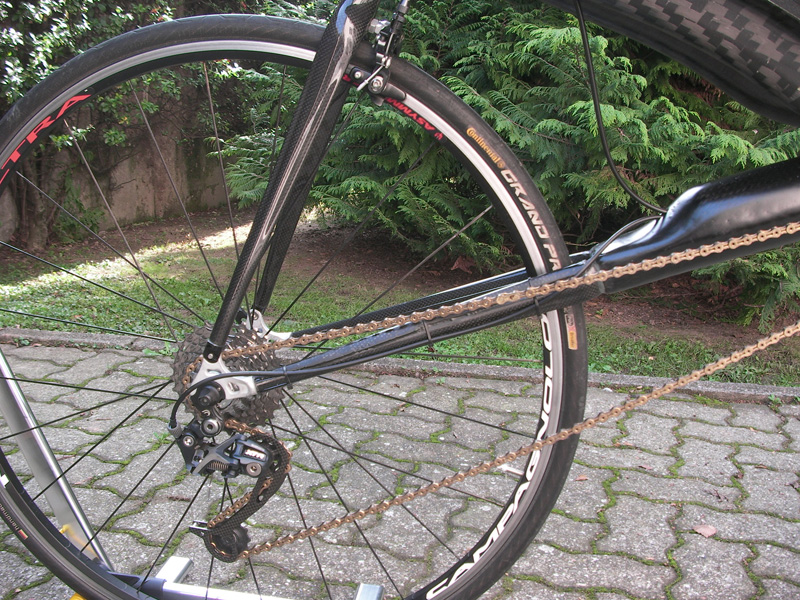
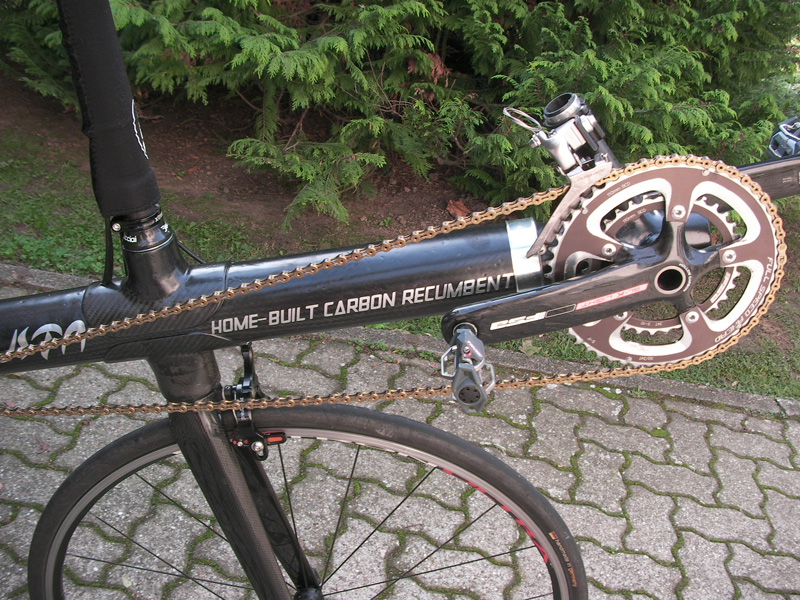
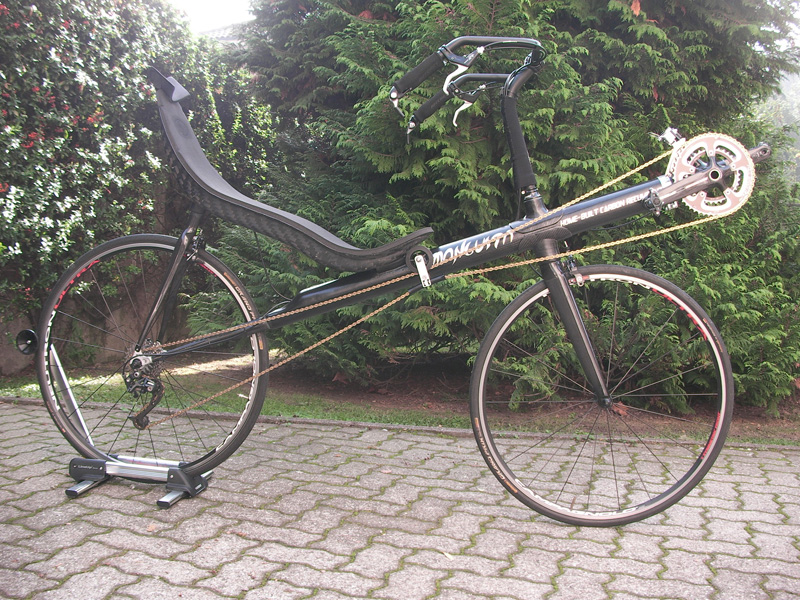
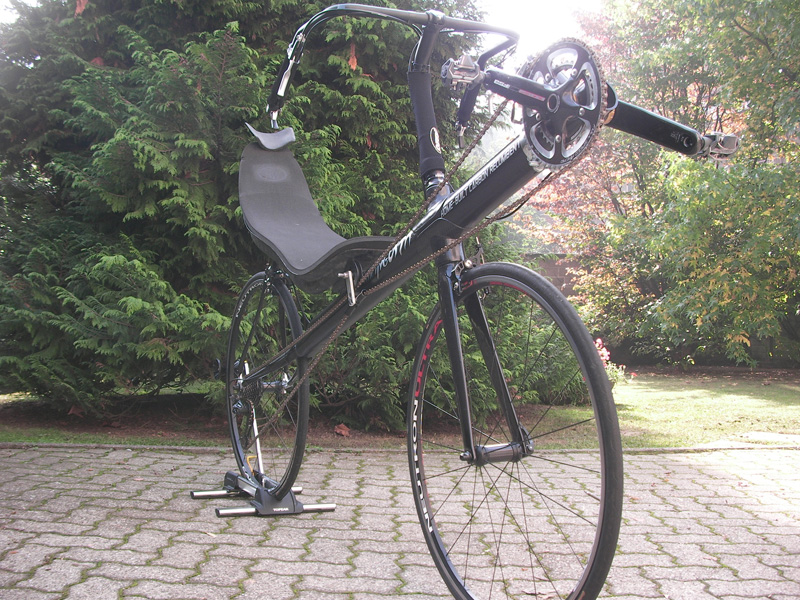
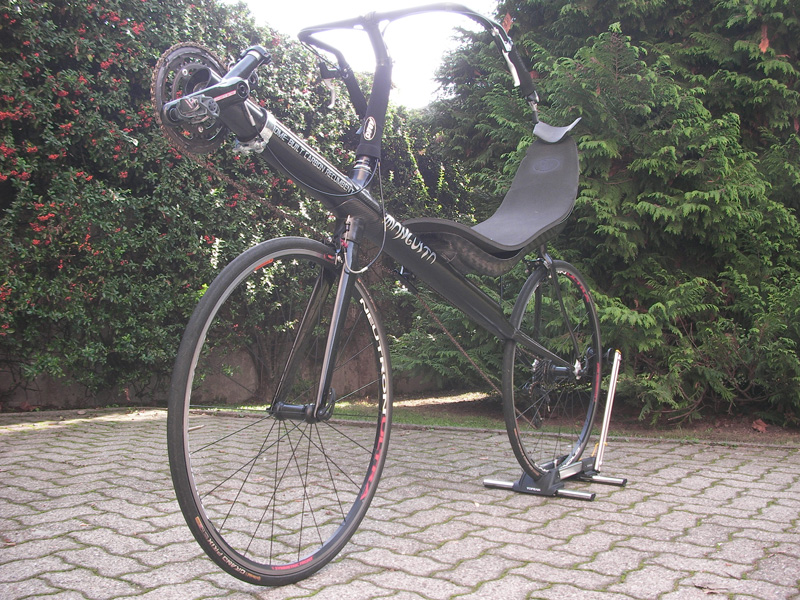
Dimenticavo, questa è la Carbent Raven originale
Edited by ninbus - 15/11/2012, 13:50